Abstract:
The
scientific inspect testing technique wire ropes
on line is a difficult problem that internal and
external science technique do not have
surmounted yet. With the development of the
modern computer and the information technique,
people have a platform for the solvable this
difficult technical problem finally.
This
article proceeds from the importance of the wire
ropes testing on line. Describing on this
platform mainly a chi eve the basic principle,
key technique, theoretical estimation of the
active service wire ropes scientific tests on
line and the real time. Quantitative results
testing on line for laboratory
Keywords:
Online wire ropes inspect testing technique
practice active service
Main
Catalogue
1.
Background (Importance, Basic Principle and
Research History)
2.
Constitution
(Sensor,
Processing Circuit Analysis Safe Ware Result
estimation)
3.
Index (Aim of Inspect Testing)
4.
Results (Laboratory Data)
5.
Reference Literature
1.
Background
(1)
Origin
The
coal mine and metallurgical mine took place the
accident for lifting the broken wire in wire
ropes. The reason is caused by internal wire
rope. Such as corrosion and broken wire etc,
flaw. That is unable discovery with the people’s
naked eyes.
(2)
Importance
The
wire ropes are a flexible component part in
extrusive application to the engineering. The
wire rope is always key component; even more it
is the lifeblood in operation. In order to
ensure wire ropes for working in safety,
reliability, higher efficiency, it is necessary
for the operation condition of the wire rope
(such as broken wire, abrasion, corrosion flaw
and metal fatigue, remainder load-carrying
ability, assurance coefficient etc.) to proceed
testing. The traditional wire rope testing
Method is artificial visual examination. This
method is that the inspectors proceed to observe
the active wire rope regularly. Adopt calipers
measure the diameter of the wire rope, feel by
hard or seek the flaw with naked eyes.
Obviously, Artificial visual examination can
only discover the bare outer part flaw (for
example broken wire), regard to the internal
flaw is powerless. It would not be examined
about the lose sight of wire ropes (or wire
ropes section) flaw with the naked eyes. And it
would be influenced relatively large by
artificial factor. The reliability of the
testing results are poor. There fore, many usage
departments for wire ropes adopt changing the
wire ropes methods regularly: According to the
rated service life for the wire ropes as certain
their changing cycle. No matter how the
practical condition is, all wire ropes carry out
changes at maturity. Obviously this can bring
some questions.
So
adopt instrument proceed testing especially
quantitative nondestructive testing is very
important. This importance express in the
following three respects.
①
Make
out from wire rope application safety
In
the course of the application, the wire ropes
can’t avoid to produce the flaw of metal fatigue
and abrasion, corrosion, deformation, rupture
etc. Thus lead to wire ropes intensity decrease.
Even be destroyed suddenly. The wire ropes take
place the destructive accident in application.
The damage of equipment. The many accidents that
the Casualties of the personnel. It was many
accidents that the typical cases are reported
publicly.
For
example, the 12 persons were killed for
ropeway-hauling rope was ruptured at Bedenmale,
Switzerland in 1972. The 4 persons were killed
for ropeway-hauling rope was ruptured at Begem,
Norway in 1974. The 43 persons were killed for
ropeway-hauling rope was ruptured at Kavale,
Italy in 1976. The wire ropes of the suspension
bridge were ruptured at Da County, Szechwan
Province, China in 1986, caused the
31Casualties. A foreign ship was at anchor in
Shanghai, China in 1987. It crashed on Baogang
Transport Material Bridge Creation huge
economical loss is caused by the fixed wire
ropes rupture out of control. Climbing ropeway
wire ropes ruptured at Tbilisi, former Soviet
Union in 1990 caused the 55 casualties. In 1990,
along-scale floating crane ship of Wu Chang
shipyard lower floating dashed upon the NO4
bridge pier of Wu han Yang tze Bridge is caused
by the fixed wire ropes ruptured out of control.
Not only it bring about tremendous economic
loss, but also bring about long-term hidden
danger of local serious internal injury in
bridge. These cases are too numerous to mention
individually. It relates to many countries and
almost all departments for the wire ropes
application. There fore, the people attach great
importance to the safety for the wire ropes in
active service.
In
order to take preventive measures. In view of
application problems for wire ropes, many
countries formulated the safety Regulations of
the corresponding trade or the state detection
standard early. But, why do the accidents being
caused by the wire rope destroys take place for
sometimes, impossible to defend effectively? It
is the important reason that is short of the
testing method and evaluation measure under
reliable wire rope condition at present, yet. At
over sea market, there have been formed many
products of the wire ropes testing for recent
years. But because of function wasn’t satisfied
with meeting the requirement of worksite
popularization application. Only a few important
departments take them as the auxiliary testing
tools proceeding the management and maintenance
for the wire ropes. The more application
departments for the wire ropes still adopt the
methods of the artificial examination and the
regular change. On the other hand because of the
accuracy and reliability of existing testing
instruments were not enough. Even if the
departments that adopt the instrument testing
wire ropes application, have taken place the
accident, such as broken wire sometimes. At
domestic manufacture, at present, the most
application departments for wire ropes adopt the
methods of the Artificial Visual Examination and
the regular change. With the result that the
accidents are happening with increasing
frequency.
②
Make
out from wire rope application economization
The
wire ropes can always produce the whole piece of
wire rope scrap for one local defeat. The
Artificial Visual examination is limited in the
attention concentration degree and experience of
the inspector. Thus the artificial visual
examination exists in the unreliability and the
localization. On the other hand appear as the
broken wire and the problems of unprecedented
concentrated corrosion etc, in the wire ropes
much more than anticipative cases for the change
of the environment and condition of the wire
rope, when the condition is serious, internal
degraded wire ropes wouldn’t be discovered from
their appearances at all. The regular change
exists in blindness this way. There fore the
Artificial Visual Examination and regular change
the wire ropes. Not only it take place the
danger of wire rope destruction potentially for
the unreliability of testing, but also bring
about enormous waste for unreason able change to
cause wire rope scrap.
In
1984, A statistical analysis made in USA of over
8,000 laboratory and field test records revealed
some interesting facts on the condition of wire
rope in services. The results make known that
approximately 10 percent of all ropes considered
showed a strength loss of over 15 percent. The
strength loss of over 20% is more than the
specified strength loss of 30%. That is to say,
the wire ropes in services, approximately 10%,
there are still potentially hazardous. More than
2 percent of the ropes had exceeded the
specified strength over 30 percent wire ropes
were in an extremely dangerous condition. On the
other hand, more than 70 percent of all ropes in
the sample were removed from service with little
of no strength loss. According to Japanese
statistical results also make known that more
than 50 percent of all ropes in the sample were
removed from service, the strength attaining
over 90 percent of the new products, even than
over 100 percent. Namely they are in running in
the period of application. In 1985, according to
the statistical results of China Coal Industry
Ministry offered these numeral: If this
instrument had been adopted for the wire ropes
state to proceed with monitor, used suitable lip
lubrication, (had been) saved, and (have been)
saved the amount of the import wire rope foreign
currency used from 20 percent to 30 percent.
③
The
Maintenance for wire ropes
The
mainest, the onerous work is the routine
examination for the maintenance of the wire
ropes in ordinary service time besides needing
lubrication. In order to guarantee the safe
operation for wire ropes, every wire ropes
application units have formulated strict rules
and regulations on the basis of corresponding
trade safe norm and the state inspection
standard. Demand practicing shift inspection,
day inspection, and week inspection month
inspection season inspection annual inspection
and emphatically overhaul institution commonly.
In the light of our country at present,
above-mentioned institution implement is all
major method with artificial visual examination.
On account of the artificial visual examination
is with the observation in the lead. The
operating speed of the wire ropes can’t too fast
in the course of the inspection. Demand under
0.3m/s commonly. But, the length of the wire
ropes application in situ is hundreds meters
long comely. Testing one time needs much time
consequently. The inspectors are easy tired, the
intension of labor is high and the efficiency is
low. This is waste of much treasure time and has
influence upon the heightening of labor force on
the other hand; the artificial visual
examination is required higher for the
operators. It would be necessary to train such
personnel for quite along time. The major
problem is that this method can only check in
slght of wire rope section with artificial
visual examination. But some flaw is given up
out of sight of the section and internal with in
the wire ropes. It can’t practice the inspection
of the whole course and completion. This become
even more decrease its testing reliability.
Thus, this is caused by wire ropes the accident
occurs frequently. For example, Dukou Mineral
affaire Bureau, Szechwan Province, China
preceded the statistics analysis about transport
ropeway accidents from 1970 to 1985. The results
make clear that the wire rope accident is 90
times. It accounts for 16 percent of the
accident sum total. It causes off the line 734
hours, 24 percent of off the line hours sum
total. Shanghai Port Authority happens with in
the machine damage accidents. Among them, about
33 percent is cause by the wire ropes accidents.
When testing the instrument. Not only the wire
ropes operating speed can heighten to several
meter per second even teen meter per second, but
also can achieve over all testing with whole
course and there fore can ensure its safe
operation, decrease the accidents, lighten the
intensity of lab our, heighten the productivity.
As
mentioned above, accidents occur frequently on
account of the wire ropes testing measures can’t
be proved effective thought practicing
item-by-item sequential inspection of the wire
ropes with much more energy and time. Even if
apare no great expense practice change
regularly. And make the user worrying about the
safety degrees. This need to proceed suitable
wire ropes in section and grant the
popularization. The inspectors judge the remnant
strength according to precise inspecting
results. Under certain conditions measured this
wire rope breaking pulling force. Master the
real safe coefficient. Not only ensure safe
operating but also determine changing date with
this method. This would benift safe operating
but also determine save the source and utilize
the source effectively. In order to achieve this
aspiration, the keys depend on the testing
method of the wire rope flaw, analysis method
and research and application for the instrument.
The
wire ropes non-destructive testing and
evaluation is that under the non-destructive
wire rope use conditions, determine the wire
rope state characteristic. With the certain
testing technique and the analysis method. And
evaluate their course according to the certain
criterion. The inspector, detecting instrument
and scrap standards are closed together
relation. According to the testing of the wire
ropes results, the inspectors determine the
remaining service life of the wire ropes and
scrap time with the inspectors experience know
ledges for giving judgment upon the wire ropes.
Among them. The testing results of the wire rope
testing instrument is the most fundamental. Only
when obtain the state of the wire rope damage
flaw can evaluate the wire rope. There fore, as
soon as the wire ropes create, the people begin
to research the wire ropes testing problems. The
wire rope non-destruction testing instruments
have been gone out of the laboratory gradually
during the past centennial research. Move toward
engineering application and go further into a
research that is combined with the engineering
application problems. At present, on account of
the continual progress of the wire ropes
manufacturing technique and widespread
application department, demand further research
and developing the testing method and achieving
technique for the wire ropes. This major express
the following several aspects.
Firstly, the rope work wire without proceeding
prestressingtorce processing. When the surface
in the wire ropes happens to broken wire, thus
reveal out of the wire ropes. This is the
obvious, also the most original method—Artificial
visual examination (foreign appellation is
rag-and visual) produce correspondingly. The
Artificial visual examination is proceeding like
this: The inspector stands by the wire ropes and
strokes them with cotton yarn in his (or her)
hand. Testing speed operate for the wire ropes.
If producing the yarn-drawing circumstances, the
inspector stops the location to observe the
broken wire carefully. However, with the
development of the produce technique and
material for the wire ropes, the rope work wire
proceeded prestressing force processing. This
makes the wire ropes to possess the astringency,
without the bedding up words. And with the
people research in a deep-going way for the
geometrical structure parameter and the service
life of the wire ropes, the structure of the
wire ropes become mare and more complex, the
flaw state of the wire ropes become to express
more and more variety and complexity. The flaw
testing difficulty increase continuously. For
example, adopting magnetic focus technique
testing the same diameter of wire ropes, Because
of the fracture magnetic force line distributed
and the fracture geometrical shape complexity,
the signal-to-noise rato (SNR) to the reverse
and the obverse twisting for the wire ropes are
different greatly. The strong signal can be
acquired in the obverse twisting, while the weak
signal can be acquired in the reverse twisting.
Even then it is submerged in the noise of ply
waves. On the other hand, the surface of the
wire rope forms the thicker fat lute for the
wire rope testing.
Secondly, the diameter of the rope work wire in
the wire ropes develop from single to various,
from single-layer ply, from circular ply to
triangle ply, and oval-shaped ply. There fore,
the evaluation of the wire ropes flaw must be
also change correspondingly. Take the wire ropes
for example, in form wire ropes with the single
diameter, can evaluate with broken wire numbers
as the target to its intensity. But in the
various diameter obvious. The influence of
intensity is the different between the thin and
thick of the broken wire. Under the
circumstances, it is unreasonable that the wire
ropes state evaluate with broken wire numbers as
the target. Have to find the other target to
wire rope state proceeding evaluation. Thirdly,
the lift system of the wire ropes develops
continuously substitute frictional lifter for
cylindrical drum hoist more and more due to
frictional lifter with the smooth advantage. The
application condition of the wire ropes hare
taken place greatly. The damage state followed
also took place greatly. In the cylindrical drum
hoist system, the wire rope express the bend
fatigue broken wire, while in the frictional
lifter, the wire ropes express the loss of the
metallic efficient cross-sectional areas. Under
the circumstances, the detecting installation
with the major target for testing broken wire
originally, must consider that how to achieve
testing problems of the wire ropes loss.
Fourthly, with the source decrease increasingly
on the surface of the earth recoverable
reserves, the depth of mineral products
exploitation increases continuously. The length
of wire rope increase continuously, the diameter
of wire rope enlarge continuously, the expenses
of the whole wire rope also increase. This
demand to enhance the safety testing of the wire
ropes, heighten testing efficiency. External
engineers experiment on the fatigue of large
diameter wire ropes. There is evidence that the
wire ropes is easier to occur in internal broken
wire and earlier than external broken wire
frequently. When finding the more external
broken wire, this means that the wire ropes
would be scrapped at once. Under the
circumstances. Because of the visualization can
do nothing about the internal broken wire of the
wire ropes, it is important that the instrument
inspect the wire ropes.
The
fifthly, because of the tourism development, the
ropeway develop rapidly in some touristy
attraction. In order to heighten the ship
passing through speed of the dike-dam, develop
shipping trade important status in the
communication and the requirement of the
communication and transportation trade
high-speed development, the number of the
cable-stayed bridges and suspension bridges are
much more and more. The wire ropes as building
bridge major component safety of their
application would be concerned the safety of the
whole bridge. And because of cable rope out side
cover in building bridge round the antiabrasion.
Put forward a new requirement for testing: In
the early part of the 20th century,
building bridges would be become the application
late period in addition. The requirement to
these bridges would be detected much more and
more.
The
sixthly, in generally speaking under all
circumstances the wire ropes application, the
produce and development of the wire ropes damage
state is a slowly varying course. But in the
course of practice application, discover the
service life shorter, scrap frequently faster
under certain circumstances. The scrap reason of
wire ropes is caused by the parameter
installation unreason-able of the whole lifting
system in this circumstance. For example,
purring the incline wire ropes hoist, if the
intervals between the idler had not been
adjusted inopportune, it would have been caused
wire ropes resonance. To accelerate wire rope
damage. There force, if the inspector can use
instrument, taking change the wire rope testing
results compare with the mystical testing
results. If the inspector discovers the abnormal
phenomena, remind the users for wire ropes
testing lifting system function parameter to
discover the problems and solve them,
immediately. Thus, attain to lengthen the
service objective life of the wire ropes. Adopt
this measures is more effective than application
later period with the instrument testing
lengthen the service life of the wire ropes, and
it is easier to attain scientific application
and arrangement for the wire ropes.
3.
The survey and the forecast for domestic and
foreign. As mentioned before, the wire ropes,
there occur testing problems form their
birthday. After the research and development of
a century, no matter where the testing principle
of the technique achievement, the wire rope
nondestructive testing research produce
development by leaps and bounds. Table 1-1 shows
that the methods and principles adopted once in
the wire ropes non-destructive testing, among of
them, some methods and principles have been
obsolete for the difficulty in technique of
principle. The following is that major introduce
several testing methods that have been used in
the engineering practice and are developed at
present.
(1)
The
Research of the Testing Principle for Wire Ropes
flaw states
The
Research work of this section is the most active
part in the wire ropes non-destructive testing,
also is the keys part.
As
one of the oldest methods, the magnetic
non-destructive testing, it is also the earliest
to apply in the wire rope testing. In 1906, the
south Africa C. Mc Can R.colson developed
together the first wire rope non-destructive
testing installation is on the basis of elector
electromagnetic magnetic principle. After
undergoing the methods of Ac (alternating
current excitation) and DC (direct current
excitation), at the present time, the wire rope
electromagnetic inspection installation become
more and more tend to adopt the permanent magnet
for wire rope the excitation. And technique
maunders gradually. It is also one of the most
widespread application methods at present. The
famous company that produce the wire ropes, such
as NDT Technology Inc, in USA, Meraster in
Poland, their products are all on the basis of
the electro magnetic inspection principle.
In
the wire ropes flaw testing and diagnosing
practice, according to the different nature and
condition of the wire ropes flaws divide them
into two large kinds: LF type (localized) and
LMA type (loss of metallic area). The concrete
character of the two flaws are as follows: LF
type flaw (Localized Fault): in the local
location of wire ropes produce damage that
include internal and external broken wire,
corrosion pots, local shape unusually. LMA type
flaw (loss of metallic Area): produce the
metallic cross-sectional areas in the wire ropes
cross-sectional areas decreasing damage that
include abrasion, corrosion, shrink of the wire
ropes diameter etc. while correspond with LF
type flaw, this kind of flaws change along
radial direction in the wire ropes slowly in
common. The major characteristic that adopt the
wire ropes testing device of the permanent
magnet excitation is that achieve LF testing
passing though local leakage magnetic field
after testing magnetization and that achieve LMA
testing passing through measuring magnetic-flux
change in magnetic circuit arrange sensitive
element. Because of the location difference in
magnetic circuit selected sensitive element,
these testing devices would be divided LMA/LF
circuit magnetic-flux testing method and LMA/LF
major magnetic-flux testing method. In the wire
ropes magnetic-flux testing method. Because of
the excitation source and the wire ropes form
close circuit, thus magnetization is easy
relatively. The circuit magnetic-flux and the
major magnetic-flux in the magnetic-flux testing
methods refer to Fig1-1 pass through circuit
magnetic-flux
Φr
in the excitation circuit. And the major
magnetic-flux of entering wire. In the LMA/LF
circuit magnetic flux testing, the wire ropes
are magnetized deep and reach the saturation
magnetization with the permanent magnet. Put the
sensitive element between the wire ropes and the
permanent magnet or at certain location in the
circuit magnetic way, measure the magnetic flux
that flow back permanent magnet from the wire
ropes passing through the air internal. This
magnetic flux is the wire ropes metallic volume
function between two pole terminals. The
inspector can measure indirectly wire ropes
average metallic cross-sectional areas between
excitation. In addition, in this testing method,
arrange the other testing devices between two
pole terminals on the neutral surface. Testing
the LF signal. LMA/LF major magnetic-flux
principle in that the wire rope are magnetized
and reach to saturation magnetization. There is
A concentric coil twining round the wire ropes.
(Caused by broken wire, abrasion, corrosion
etc), can lead to change of the major magnetic
flux in the wire ropes. After passing through
the integrator alternate, the output of the
integrator between the major magnetic flux
change proportionally. There fore, only when
measure the change of V1 cans you achieve the
change measure of LMA.
At
present, there two testing methods in LMA;
Because of the bulky volume with the testing
method of LMA/LF circuit magnetic-flux and
radial direction resolving property is lower
(51cm). This method has been obsolete
gradually. While because of the definition
higher of radial direction (4cm) at testing LMA
time with LMA/LF major magnetic-flux method.
Part of LF flaws can also reflect and approach
the wire ropes state evaluation from the
perspective of great practical significant than
the signal of LF is. The signal of LMA is
greater especially; the split coil would be
solved technically. And pass signal-processing
circuit of designing structure unique; achieve
the absolute magnitude measure of the wire ropes
magnetic flux. Make the testing method of LMA/LF
major magnetic-flux extensive application for
the wire ropes in situ testing
Table
1-1 The Wire Rope Nom-destructive Testing
Principle
Methods |
Measure Principle |
Expressing pattern |
Advantage |
Shortcoming |
remarks |
Solid sound testing method |
Record the longitudinal pulse quantity
when the broken wire occur |
Line of diagram |
Can automatic recording broken wire
continuously |
At present, only apply to the laboratory
the cost of instruction is higher |
It is adopted when the broken wire only
occur |
Aeroacoustics method |
Record the acoustic signals, when the
broken wire occur |
Line ditto |
The cost of instrument is lower and can
automatic recording broken wire
continuously |
It is difficult to prevent from the
other influence of disturbance sound. At
present, only apply to the laboratory |
It is adopted when the broken wire only
occur ditto |
Artificial visual examination method |
With under 0.3m/s of speed inspect the
surface of the wire ropes |
Without automatic record, analysis
results directly |
A simple easy method and can ascertain
the damage of the surface |
A is waster the time, without object,
science. Grease effect accuracy of
result |
Up to now have been used abroad. |
Optical method |
CCD camera shooting head testing the
surface of the wire ropes |
Picture |
Testing accuracy is higher |
The cost of equipment is higher and
influenced by grease |
Detect the diameter. Of the wire rope
successfully |
Acoustical method |
Rnock at the wire ropes |
Without automatic record, analysis
results directly |
A simply easy method
|
Measure is unilateral and expressiveness
is poor. |
Major application is that the inspector
evaluation corrosion of the wire rope |
Machinery method |
Determine the resilience of the wire
ropes loading and length with testing |
Data |
|
Both exerting stress and length are
difficult to master accurately |
|
Magnetically method |
Determine the leakage magnetic-field |
Line of diagram |
Can determine the broken wire, corrosion
sopot, distortion |
When the corrosion, abrasion, broken
wire come into existence at the same
time. It is difficult to distinguish
them |
At present it would be mature md use
abroad. |
Measure the major magnetic-flux |
Ditto |
Can determine the change of metallic
cross-sectional areas for the wire ropes |
Can’t suit testing broken wire
|
Ditto |
Magnetically imagery |
Picture |
Can orient ate broken wire, corrosion
area accurately |
The structure is complex and the picture
explanation isn’t unique |
At present only apply to the cob
oratory |
x-ray |
|
Take a photogram |
Can know broken wire accurately |
The cost of protective installation is
higher. And can’t measure continuously
for long time exposure |
|
Methods |
Measure Principle |
Expressive pattern |
Advantage |
Shortcoming |
Remarks |
Sonic launch method |
Determine wire rope launching supersonic
waves when wire rope structure take
place changes |
Tran audient analysis |
|
The cost of instrument is big her, can
only use in the quiescent load part
|
|
Supersonic method |
The supersonic wave disseminate in the
mediums |
Reflect gram |
|
Can’t reflect the wire ropes state in
detail with existing reflect of every
wire rope |
|
Magneto striation method
|
Magnetostrictive effect
|
Line of diagram |
Non-cross block measure, can inspect
within 100m, the flaw of the wire ropes
for once. |
The definition and detection rate is
poor for small fracture and flaw change
|
|
Electrical eddy-current method |
Electrical eddy-current effect |
Ditto |
Can inspect broken wire, fracture,
corrosion in the wire ropes |
Tendency surface effect in fluence the
broken wire testing. The signal to noise
rato (SNR) is lower. |
|
Electrical current method |
Determine ohm age of fixing wire rope
length |
Line of diagram or data |
Can ascertain fracture surface state |
It is difficult to master the end
stress, temperature and prolongation for
the moving wire ropes |
|
Vibration testing method |
Transversal excited vibration waves
dffeminate in the wire ropes
|
Lin of diagram |
Can inspect the change area of cross
sectional area for the wire ropes |
Flaw definition poor |
|
In LF
testing, at first, adopt the inductance coil
testing leakage magnetic field in the wire
ropes. But because the output signal in coil
come under the influence of relative speed
change between the wire ropes and the coils
greatly. This testing method has been obsolete
gradually. Because of the development of the
semiconductor technique, Magnograph series
sensors in Canada, at first, adopted hall device
inspect the leakage magnetic-field and applied
for a patent in the late seventies Canadian
rotes co graph sensor adopted the fluxgate
technique achieved the signal collection of the
wire rope LF flaw for avoiding violate patent of
Magnograph in the ignites. Domestic technique,
middle China science and engineering university
and Shanghai mercantile marine institute adopted
the integrated hall device and the fluxgate
achieved the signal attainments of LF flaw
individually.
Whether the circuit magnetic-flux inspect or
whether the major magnetic-flux of LMA/LF
inspect, if you want to require the flaw
information for the wire ropes, the wire ropes
must pass through the sensor. This cause wire
ropes whole course testing to be difficult to
achieve. In order to solve this problem, in
1994, H.K wan and C.M Teller at American
Southwest Research put forward a kind of new
type wire ropes flaw testing sensor that is on
the basis of Magnetostrictive effect
(Magnetostrictive Sensor, Mss) The basic testing
principles, as shown in Fig 1-2 (8)
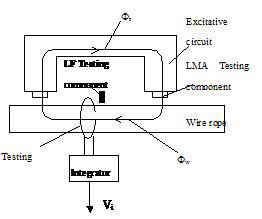
Each
sensor includes a permanent magnet and a
inductance coil. The permanent magnet provides a
biasing magnetic field to ensure the sensitivity
of sensor and electric is the same with
mechanical wave spread along the wire rope axial
direction. After the launching coil is
stimulated by the pulse signal with the Pulser,
the joule effect productive wave would spread
along the wire rope axial direction. When the
mechanical wave pass through receiving coil,
because of villain effect. If there occur flaw
signal, receiving coil can accept the return
waves of flaw signal. In this way can achieve
the wire ropes flaw testing. Because of existing
initiative testing method, the time is shorter.
The effectiveness is higher. According to the
two scholars tentative experiment, testing 100m
length wirer ropes need only several seconds.
At
present, have the major difficulty in the
following two respects for this testing method:
(1)
The
Difficulty in Physics Field,
Nowadays don’t make a deep research on the
mechanical wave mechanization of
Magnetostrictive effect creation and trans
missive characteristic.
(2)
The Difficulty in Technique
According to the tentative research results. It
is very wide that the Magnetostrictive effect
causes the signal frequency band from several
KH2 to 1m. How to collect this signal is that
practical application must be solved the
problem. If the two tough jobs were broke, this
would be had a great future testing method.
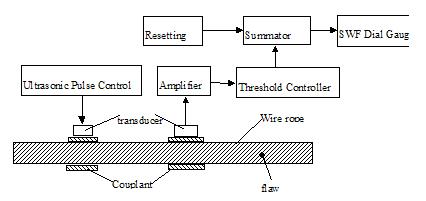
At
abroad, the Acousto-ultrasonic method is being
adopted to achieve for the wire rope state
testing on line. Now (9.10.11.12) besides the
magnetic testing method. The basic testing
principle ad shown in Fig. 1-3
The
method is development on the basis of the
original sonic launch method. Lead the sonic
into wire ropes with a group of transducer,
couplant. The imitative sonic launching specific
property transmits in the wire rope. The other
group of, conplant collect the signal, after
passing amplifier enter the threshold controller
and then calculate the stress-wave factor (SWF).
Because of comprehension with sonic launch and
ultrasonic two methods. Not only can proceed to
the flaw inspection, flaw imagery, and flaw
characteristic, but also can evaluate the
inherent function of the testing wire ropes
online. Such as the fatigue loss, intensity,
hardness etc, for wire ropes.
This
method can have application in dynamic state
wire rope testing. It overcomes that the sonic
launching method can only have application in
static state wire rope testing and catch the
instantaneous signal of the broken wire
breakage, without enough.
Above-mentioned methods have main application in
the material function of wire rope testing. At
present the all of the world, are proceed to
research the geometrical deformation of wire
ropes loose ply testing etc. German SPK Company
try to adopt the CCD device testing the diameter
of the wire ropes. For the change of the wire
ropes. American adopt artificiality knock at the
wire ropes with hammer in their hands to
discover the loose ply flaw.
(2)
The
Analysis Process for Wire Ropes flaw Signal
After
the flaw signal of wire roper is colleted by the
sensor with the certain principles and methods.
The analysis process measure of signal is also
very important. The simplest method is that to
show the signal on the oscilloscope. But is
can’t store to provide analysis application
later. In order to over come this flaw, can
adopt the notebook recording instrument or tape
recording instrument. The wire rope testing
instrument of earlier period adopted all these
methods such as Magnograph and LMA series flaw
detector. Up to the eighties, with the
high-speed development of the computer technique
and digital handling technique, the
computerization and visualization of the testing
instrument the came a development tendency. With
the signal of the wire rope testing processing
because of the signal of LMA and LF existing
different testing principle and signal
characteristic, the signal processing adopted
the different technique. In 1978 at Poland,
researcher carried out experiment research,
adopt three testing circuit, to collect the
signal of the wire rope cross0sectional area
loss, and then after passing A/D transform,
achieve the digitalization.
According to the establishing model calculate
the cross-section of the wire rope loss and chi
splay on the computer’s screen. First of all a
chi eve the quantitative handling. The domestic
technique, Middle China science and Engineering
University achieved the quantitative testing of
the wire rope broken wire numbers, in the
eighties. With the adopting equally spaced
interval sampling technique and differential
super threshold algorithm. In 1995 Japanese
scholar Koichi Hana Sake and Kazuhiko Tsukada
introduced image formation technique into the
signal handling of the wire ropes. At first
achieved the visualized testing of parallel wire
rope broken wire.
American, Doctor H.R. Weischedel combine with
the worksite application condition to the signal
testing of LMA. Testing the signal size of wire
rope LMA within the speed limits has nothing to
do with the operating speed for the wire ropes
with designing the split coil and the electric
circuit structure of the new and original
structure. And adopt a certain calibrating
pattern achieve the quantitative testing of LMA.
In Poland, K,Zawada introduced the personal
computer Memory Card Internatonal Association
(PCMCIA) standard in to the manufacturing
standard of the wire rope testing instrument.
Because of the high reliability, antimagnetic,
powerful applicability, provide a way for the
wire ropes testing instrument toward engineering
application. At present, in Poland, MD series
wire rope inspection instrument inter face in
Meraster Company, all adopted this standard.
(3)
The standard of the Wire Ropes non-destructive
Testing evaluation and the Instrument Testing
It
includes the contents of the two sides, one is
the testing signal evaluation, the other is that
it evaluates the wire ropes states for the
testing results; evaluation of the testing
signal is also evaluation for the testing
instrument. It includes the index of the
instrument definition, quantitative definition,
penetrating power; signal-to-noise rato of
testing signal is lower. Can’t be quantitative
testing ability. After leading to the computer
technique, achieve the quantitative analysis and
handling for the wire rope flaw signal. At
present, because of the wire rope quantitative
testing technique mature day by day, and the
results of testing can be evaluated for the wire
rope state. Because of the wirer rope state
evaluation is major evaluating the intensity of
the wire ropes. But existing testing instrument
can’t test the intensity of the wire rope
directly. Because of the results of testing are
related to the scrap standard of the wire ropes
frequently. It is often necessary to introduce
the personal factor, to the wire rope inspector
is familiar with the instrument function and
applied state.
At
present, the scrap standard of the wire ropes
make on the basis of breaking stress for the
wire ropes. But mechanical function research of
the wire ropes express this method unreliability
in resent years. There fore, according to the
present scrap standard of the wire rope with the
results of testing, evaluating method to the
wire ropes state become more and more
unreliable. American NDT Technology Company is
on the basis of the wire rope inspecting
installation of LMA-LFTM type,
combine with the worksite application condition
in the installation and the Artificial visual
examination results. Put forward now to
evaluating the method of the wire ropes
intensity.
American inspection and material Association
worked out the Electromagnetic Examination
Standard of Ferromagnetic material steel wire
rope (E 1571-96) in 1997. this is symbolic of
the testing and evaluation have enter a brand
new stage for the wire rope.
2.
The constitution for the wire ropes inspecting
installation
According to the peculiarity in coalmine
application, the basic principle of the testing
wire ropes adopts the magnetic non-destructive
testing method. There is inspecting sensor,
signal preprocessor, analog digital converter,
sampling controller, computer analysis handling
system etc several main component parts in major
inspecting installation. The basic block diagram
as shown in Fig. 2-1
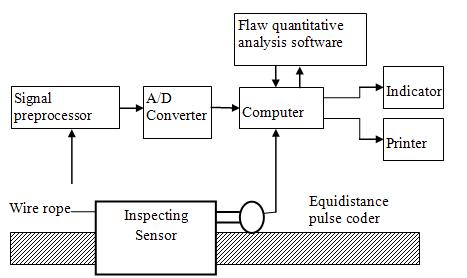
Fig.
2-1a Wire Rope Flaw Testing System for Three
Gorges Ship lift
The
sensor adopts two different magnetic testing
methods inspect the broken wire and the loss of
the cross-sectional areas for the wire ropes.
Among them, broken wire testing sensor would
export two way-signals individually. The signal
is alternating current signal. Connect
alternating current signal amplifier. The sensor
of the cross-sectional areas loss testing would
export two way-signals individually. The signal
is direct current signal. Connect direct current
signal amplifier later, multiple-path different
nature signals pass through A/D converter later
with computer, proceed to proceeding to
analyzing handling, controlling sensor signal
sampling is sampling controller. According to
the sensor relevant wire rope operating length
send out sampling pulse, control to sample the
output signals of the two sensors individually.
Among them, interspaced of broken wire signal
sampling is less than the signal of the diameter
testing. While the signal of the diameter
testing is less than testing signal of the
cross-sectional areas loss. It is between from
1mm to 10mm in general.
The
following is that introduce the testing system
combining with the main technique difficult
point.
(1)
Development of the sensor
① The
Magnetic problems for wire ropes
According to the knowable technique as analyzed
before, adopt the magnetic testing method
inspect the same time, with the development of
the permanent magnet material, adopting the
smallest volume permanent magnet can put forward
very strong magnetic field to be satisfied with
the necessity of wire rope magnetization. There
fore, testing wire rope method become more and
more tended to adopt the permanent magnet
achieving wire rope magnetization. Fig. 2-2 is
that adopt the magnetic circuit in the small
diameter wire rope testing. Because of smaller
diameter for wire rope, the magnetized volume is
smaller, correspond entry. At the Sam time.
In
order to ensure the wire ropes magnetic
uniformity, take increasing pole terminal method
between the wire ropes and the permanent magnet,
on the other hard, can also adopt method to
parallel with the multi-piece permanent magnet.
Increase magnetic flux in the wire ropes;
achieve the wire ropes magnetic requirement. In
face, adopt circumferential single circuit axial
magnetization for wire ropes. Because of each
circumferential part for the wire ropes being
different from the permanent distance, the
magnetization for wire ropes is non-uniform.
Near the permanent magnet parts magnetic field
intensity is higher, on the opposite side parts
magnetization degree is lower in general. In
spite of the pole terminals were adopted, can
decrease this non-uniformity in certain degree.
With the enlargement of the wire rope diameter,
the non-uniformity distributed of the magnetic
field become more and more obvious under the
extreme circumstances, near the permanent magnet
parts can inspect the signal obviously. On the
opposite side parts can’t inspect the signal.
There fore, to large diameter wire rope
magnetization can’t adopt single circuit
exciting way, must adopt circumferential
multi-circuit axial exciting magnetization way
manly. Because of the nonlinearity and vector
characteristic for magnetic field, the magnetic
intensity in the wire ropes can’t increase after
the multi-magnetic field superimposition. There
fore, when designing magnetic circuit, must
distribute magnetic circuit reasonably. Ensure
the multi-circuit magnetic effect. In the
initial stage of experiment, have application in
double circuit for small diameter wire rope
proceeding excitation in imitation of single
circuit excitation way. With the result that
instead of increasing, the broken wire of the
wire ropes even decreasing. And the signal is
instability. These phenomenon express the
multi-circuit magnetization can’t design in the
light of the single circuit magnetic way simply.
This is conforming to the theoretical analysis
as mentioned before. At present, the key problem
is that find the reason that the magnetic line
distribute the magnetic circuit aspect.
When
analyzing to adopt double circuit magnetization,
the magnetic line distribute as shown in Fig.
2-3 Because of existing the pole terminals,
couple up magnetic line of up and down two
magnetic circuit with the pole terminals, form
the magnetic line of the certain direction
concentrating pole terminals areas. It becomes a
magnetic source that forms the magnetic line
with armature closing up on the other end
surface magnetic line. At the same time, in
order to ensure the wire ropes magnetic
uniformity. The volume of the pole terminals is
larger generally. In this way, the pole
terminals is magnetized by the permanent magnet
providing a great deal magnetic power, not by
the wire ropes. In order to achieve the
multi-circuit magnetization it is impossible to
increase (or decrease) the volume of the pole
terminals between the wire ropes and the
permanent magnet.
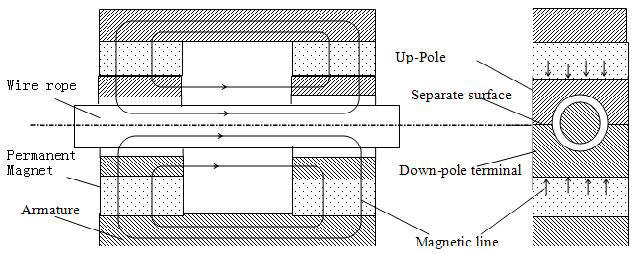
In
order to test and verify the correctness of
above-mentioned analysis, proceed with
experiment.
1) At
first, make an experiment on a 24mm diameter
steel stick the experimental installation as
shown in Fig. 2-4. At first, adopt single
circuit excitation. Detecting magnetic induction
intensity’s are all 0.48T in measure point A,B
individually. And then add as shown in dotted
line excitation circuit. The whole system forms
a double circuit excitation structure. At that
time, detecting magnetic induction intensities
are 0.73T and 0.75T in measure point A,B
individually. This express that increasing
magnetic circuit can be heightened magnetic
intensity in the magnetic stick. During
proceeding with sensor structure design, it is
impossible for us to adopt magnet adjoining
steel stick structure way. There must be a
distance between magnet and steel stick. In
order to imitate this condition, at first as
shown in Fig.
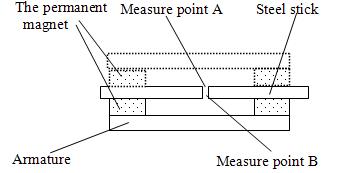
The
magnetic circuit of active line. Add a 5mm
thickness aluminum plate because of
non-permeability magnetic material. At that
time, detecting magnetic induction intensities
are 0.69T and 0/74T. Obviously, it is unlike for
you to imagine the magnetic induction
intensities of A point is mare than B point,
even if the magnetic inductor intensities of
these two measure points are all decreased.
After adding a aluminum plate in dotted line
magnetic circuit, detecting magnetic induction
intensities are 0.66T and 0.67T individually.
Even if after adding the distance between magnet
and steel stick, the magnetic intensity is
decreasing. But it is still more power than
single circuit magnetic intensity. In addition,
increment of magnetic circuit they exist the
nonlinearity and vector characteristic, we can
find the change condition from the whole
magnetic induction intensity of magnetic circuit
measure point. This require us to design the
magnetic circuit must pay attention to have a
subtle difference between the magnetic circuit;
otherwise it is easy to lead to magnetic circuit
design failure.
2) In
experiment 1, we consider only magnetic circuit
symmetrical condition; consider the non-symmetry
condition in the following. In the laboratory,
make an experiment on a 90mm diameter steel
stick. Experimental installation as show in Fig.
2-5. during the experiment, add the condition of
magnetic circuit as show in order number, detect
experimental data as show in table. After adding
a 5mm thick ness aluminum plate in excitation
circuit, detect experimental data as show in
table2.
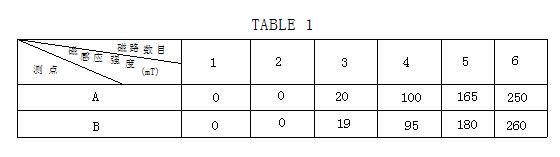 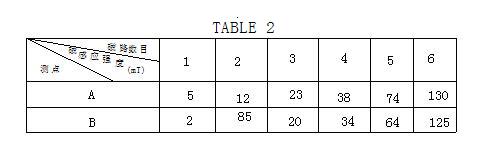
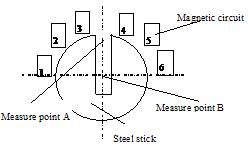
Fig.
2-5
Φ80mm
steel stick magnetic Experiment Installation
Make
out from the experimental data of table 1 and
table 2: To large diameter of steel stick,
muti-circuit excitation can increase magnetic
intensity obviously. Whether the wire ropes from
above mentioned experimental scheme is employed
or not, still test and verify with experiment.
According to the above-mentioned structure
design sensor make a magnetic intensive
experiment or 52mm, 90mm diameter for the wire
ropes. With the result that the magnetic
intensity of the wire ropes testing. The
above-mentioned experimental express that it is
feasible to adopt the circumferential
multi-circuit axial exciting magnetization.
②
The
acquirement for broken wire signal of the wire
ropes
1)
The
difficult point for broken wire signal
acquirement
The
exciting installation magnetizes the wire rope
to certain magnetic field intensity; adopt the
permanent magnet as exciting source. Leakage
magnetic testing installation inspects the
broken wire producing diffusive leakage magnetic
field. There are inductance coils, hall device,
magneto sensitive transistor etc, application in
the magneto sensitive testing sensor of this
kind magnetic field testing.
When
the induced coil test, induced output voltage
changes with Cole scanning speed change. The
temperature drift of magneto sensitive
transistor effect is greater; there fore the
hall device for Hall effect is more advance in
testing this kind of magnetic field. The
inspecting sensor is composed of exciting
installation and leakage magnetic testing
installation when testing the wire ropes, must
consider the following three questions:
(a)
According to leakage magnetic field testing
principle of the wire rope broken wire, can be
knowable for the single piece of wire rope
diameter is thicker in 6×7
structure wire rope. At that time, the broken
wire signal is easy to obtain for the single
piece of wire rope produce the leakage magnetic
field growth. But according to the experiment,
the distances between strand peak and strand
wave is growth as the wire rope diameter
increase. And the relative location between the
wire rope strands is easy to become deformed, as
the wire rope diameter increase. As a result
cause that the broken wire signal is very easy
to inundate with the strand wave signals. Fig.
2-6 is the strand wave signals of 6×7
structure wire ropes. In Fig. Section a and
section is normal strand wave signal, section b
is that the signal form with the wire rope ply
strand and the distance growth between wire
strands. Besides, there is a burr signal in the
signal cu. This is formed with the leakage
magnetic field between the wire ropes for the
diameter of the wire ropes.
(b)
In order to ensure no miss testing, must install
multiple component along the wire rope
circumference for the diameter of wire rope
growth and the circumferential covering area
limited of the single component installing
component number can be calculated as follows.
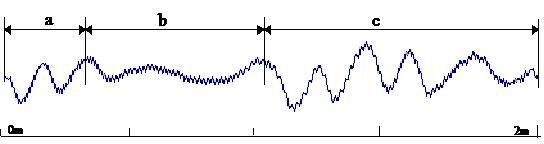
wire rope length
Fig 2-6 Wire rope
stock wave signal
Where Sp is the perimeter of component
arrangement ring,
Ss is the circumferential covering length of the
single component
CINT[·]
is round off number
According to the circumferential covering are
length is 7mm, if the diameter of wire rope is
30mm, must arrange at least 14 components along
circumferential direction can achieve no missing
the testing. As that time adopted the single
component handling, it was very complex.
(c)
The wire rope fracture out diffusion leakage
magnetic field intensity attenuate from fracture
location out ward as space negative index. There
fore, the magneto sensitive component can
inspect the internal broken wire intensity very
weak. On the other hand, the broken wire in
inlayer produce the magnetic field to become
weaker for outer wire rope screening effete.
2)
Magnetic Focus Testing Technique
In
accordance with the above-mentional character,
the broken wire testing in view of the magnetic
focus testing technique, inspect the leakage
magnetic field in the different adecker wire
rope broken wire creating leakage magnetic
field. The magnetic focus testing principle is
as shown in Fig. 2-7
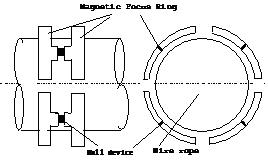 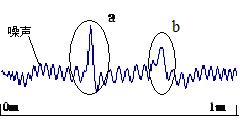
The
magnetic focus ring of uniform-distillated
circumference collects the Hall device making
hall device detecting average magnetic field
with in the following four points mainly:
(a)
the magnetic focus ring adopt the high
permeability materials manufacture, such as
industrial clean iron, perm alloy. They collects
weak magnetic field with the wire rope fracture
creating out diffusion circumference, increase
the testing sensitivity. The experience express,
the sensitivity can heighten over 10 times as
compared with single Hall device testing.
(b)
In order to prevent from missing testing, it is
necessary to arrange a great deal components
along circumference usually for the single Hall
device scanning areas are limited along wire
rope circumferential coverage. This wand
increases the complexity in detecting sensor and
follow-up signal handling system. After adopting
the magnetic focus ring, would enlarge the
scanning range of single component. There fore,
using few components such as two or four can be
achieved the no missing testing for the leakage
magnetic field.
(c)
There occurs homogeneous influence in the
magnetic focus ring toward magnetic field. There
fore after adopting the magnetic focus ring,
would homogenize the leakage magnetic field
between the wires and strands in the wire ropes
to heighten the sound-noise rate of the testing
signal.
(d)
Arrange the each magnetic focus ring with a
piece of Hall deice, and a piece of Hall device
deals with independent channel. Thus, can
distinguish the broken wire in the different
locating and layers. As shown in Fig. 2-8, adopt
the above-mentional testing method detecting the
output signal curve on the surface of wire rope
and the certain channel in the internal core
wire broken wire testing. In the Fig, a,b
location is the signal curve of a piece of outer
broken wire and a piece of internal broken wire
individually.
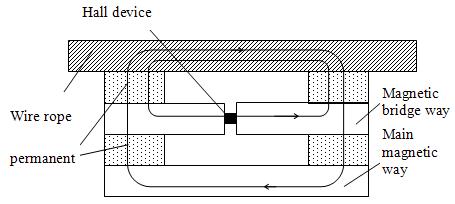 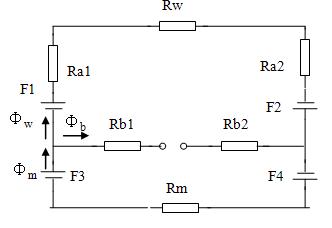
Magnetic bridge
circuit equivalent magnetic circuit model
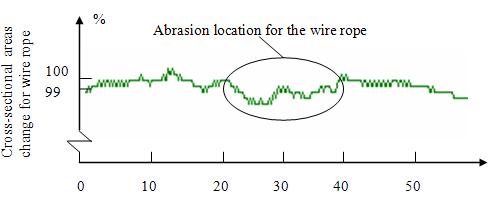
③
The inspecting method for abrasion signal
Under
the ordinary circumstances, the abrasion testing
of the wire rope adopt the testing main
magnetic-flux method. The testing component
adopt testing coil unusually. This brings the
two problems for wire rope testing in situ.
1)
The trouble of the sensor installation is caused
by the coil twining the wire rope.
2)
The sensitivity of testing coil is relevant with
the operating speed of wire rope relative to the
coil. Adopting the Hall-device testing magnetic
field possess the advantage without speed
influence. And can acquire absolute magnitude
for the magnetic field. But, when the Hall
device was put in magnetic wire rope main
magnetic circuit testing directly, the Hall
device output signal the saturation wouldn’t be
susceptible to the tiny change in magnetic field
for the magnetic inductive intensity great (in
general from 0.6T to 1.0T). for this reason, put
forward utilizing the inspection principle for
magnetic bridge circuit magnetic way, place the
Hall device in magnetic bridge way, testing the
tiny change for the magnetic inductive intensity
in the balance point, (the magnetic inductive
intensity is with in
±100mT
in common) to ensure Hall device high
sensitivity and linearity. The basic principle
as shown in Fig. 2-9.
The
main magnetic way and the bridge way combine
action magnetizing the wire rope to reach the
saturation degree. Because of the wire rope and
the main magnetic way being symmetrical about
magnetic bridge way, can’t consider the
influence of leakage magnetic flux. According to
kirchhoff principle for magnetic circuit. This
is,
Φm=Φw+Φb
(2-2)
WhereΦb
is the magnetic flux in the magnetic bridge
circuit
Φb=BbSb
among them,
BbSb
are magnetic inductive intensity and
cross-sectional areas in magnetic bridge way
individually:
Φm
is the magnetic flux in the main magnetic way.
Φm=BmSm
among them,
Bm,
Sm
are magnetic inductive intensity and
cross-sectional areas in the wire rope,
Φw=BwSw,
among them,
Bw,Sw
are magnetic inductive intensity and
cross-sectional areas. In the wire ropes, take
above-equation substitute (1) after arrangement,
obtain the equation we may write the equation.
Sw=(BmSm-BbSb)/Bw (2-3)
Here,
the magnetic inductive intensity
Bw
in the wire rope and the magnetic inductive
intensity
Bm
in the main magnetic circuit are constant value
near saturable magnetic degree. The
cross-sectional areas for the main magnetic way
Sm are decided by design. There fore, make out
from the equation (2-3) the cross-sectional
areas of the wire rope Sw and Bb related to
linearity.
Under
the ordinary circumstances, the wire rope is
identical with magnetic field parameter in main
magnetic circuit; through the magnetic flux in
magnetic bridge circuit is zero. When the
cross-stctional areas for the wire rope change,
the balance of the whole magnetic circuit system
is broken. The magnetic flux in the bridge way
isn’t zero. After testing Bb, the
cross-sectional areas Sw can be acquired from
equation (2) calculation. The Fig. 2-10 Sw is
given by the following. Technique.
Fig 2-14Software system diagram
Adopt in this prinuple designed sensor collect
abrasion signal curve of wire rope in the
certain mine lifting wire rope
(2)
The handling electric circuit for detection
signal
①
The pre-handling electric circuit for detection
signal
The
electric circuit principle is shown in Fig.
2-12, the electric circuit principle is shown in
Fig.2-13
The
electric circuit is composed of the signal
coupling, amplification, low-pass filtration and
reshaping etc. link.
In
order to restrain the work electrical power
disturbance in worksite situ, the electrical
power of signal handling installation adopt the
supply power pattern with PC/DC second regulated
power supply voltage stabilizer to heighten the
sound-noise rate and stability of detection
signal. The signal handling circuit possesses
the function as follow.
1)
Can pick up the weak signal that the testing
component sends from the noise background, the
sound-noise rate for testing signal is over
34dB.
2)
Can handle the multichannel-testing signal, each
handling channel for testing signal doesn’t
disturb each other.
3)
Every channel can adjust the zero drift of
amplifier and the gain of the amplifier.
4)
Can adjust pass band in wave filter.
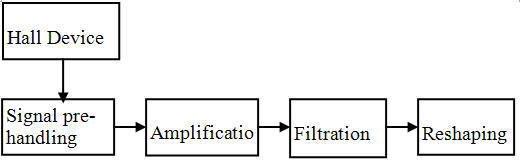 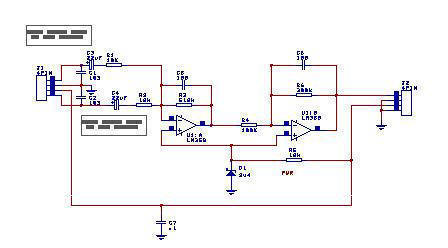
③
Data
sampling board Selection
The
function of A/D trans form is that the sensor
with pre-handle send the analogue signal
changing the digital signal of available
computer handling to achieve quantitative
analysis of flaw providing foundation. When
choosing A/D, must consider the precision and
time of trans form, channel number etc. Here,
after consideration every aspect factor, select
the PCL-818C A/D board of Taiwan Yanhua company
Products. The A/D board is on the basis of IBM
PC/XT/AT or data sampling board with
high-function multifunction in compatible
machine. It is possessed of feature as follow.
1)
Can select 16 channels single-ended or 8
channels double-ended
2)
Analogue quantity input
The
twelve-digit number A/D trans form precision
adopt DMA when data Tran missive pattern of
different amplificative gain, the single channel
sampling frequency can use 40Khz.
3)
The software programming can adjust the multiple
of gain.
4)
The software can install A/D quantity size
5)
Provide trigger of the software, internal clock
and outer A/D Tran missive pattern
Besides, the A/D board can connect the PCLD-8115
signal adjustable board with Yinhua company
products. The signal adjustable board provides
temperature compensation circuit can restrain
temperature drift for signal influence
(3)
The development of analysis software for signal
quantity
.The
software block diagram for the wire rope flaw
quantitative analysis system is as shown in Fig.
2-14 parts of function brief introduction as
follow.
Calibration
——testing for broken wire. Ascertain threshold
value.
Achieve the quantitative analysis
for wire rope broken wire.
Parameter
installation——Provide different structure wire rope parameter
and the
Quantitative analysis required parameter.
Sampling
on line——When the sensor moves along the wire rope, the
optical code
Wheel
sends the outer-triggered signal; take the
signal of the sensor into the computer,
Achieve space sampling for the testing signal.
Ensure the quantitative analysis.
Historical
data——Proceed to analysis offline for sampling signal
in the past
Historical
result——Proceed to display again for analysis results in
the past
Wave
analysis——Proceed to wave display for sampling signal,
under this state,
pushing the key F, can print the displaying
wave.
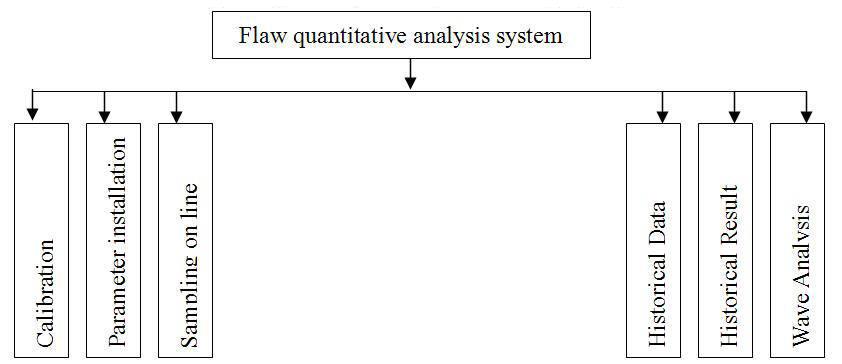
Fig.
2-14 software system Block Diagram
②
The quantitative analysis for abrasion flaw
According to the magnetic bridge circuit testing
principle, can know that the metallic
cross-sectional areas for the wire rope Sw is Sw=(BmSm-BbSb)/Bw,
there fore, after the sensor inspect Bb, the
cross-sectional areas of the wire rope Sw can be
get from above equation.
The
abrasion of the wire rope is corresponding with
the change quantity of magnetic flux. In fact,
it is absolute change in whole magnetic flux of
magnetic circuit variance. With above
theoretical analyses can know that it is
relevant with in proportion between the abrasion
quantity and signal amplitude of wire rope. In
order to ensure the sensor in the course of
practical testing, possess the testing areas as
large as possible, for the component is liner
with out put in
±100mT.
At the sensor design stage, would ensure
magnetic feature in the main magnetic circuit is
consistent with magnetic feature in wire rope
testing soon. This means that make the
magnetic-flux near zero passing through balance
magnetic circuit. The metallic cross-sectional
areas of the wire rope change very great for the
different structure and technology of wire rope.
Proceed to influence very great for magnetic
circuit feature of the whole testing
installation. The testing result isn’t accurate.
There fore, before testing the wire rope, must
calibrate the sensor. Namely, put the new wire
rope without abrasion, into the sensor. The type
of this wire rope is consistent with the
diameter, material etc. Of testing wire rope.
During the operating course, unload change,
stretcher strain deformation have influence on
the cross-sectional areas of wire rope for the
wire rope is a elastic component.
It is
require that the testing installation must
calibrate testing online. Developed inspection
installation provides two different calibration
methods to counter different application state.
After the whole lifting system install adjusts,
proceed to testing for new wire rope testing
online. There fore, select at time, testing
result is compared with the basis point to
acquire the state of wire rope relative
abrasion. In general speaking, adopt the
preceding method is more accurate to acquire the
abrasion state of the wire rope.
Besides, the abrasion testing of wire rope is to
measure the absolute intensity of magnetic field
in the magnetic circuit in fact. The measuring
is each point abrasive size actually. The
leakage magnetic field has great influence on
testing result for the deformation and the
broken wire. For this reason, must adopt the
smoothing technique in software to decrease the
influence of abrupt change leakage magnetic
field. The Fig from 2-16 to 2-18 is the
quantitative output results for abrasion
testing.
③
The quantitative testing for rustiness
The
rustiness for wire rope can be divided into two
kind of pitting and corrosion. The rustiness
leads to the decrees of the efficacious metallic
cross-sectional areas. Not only breaking load
would decrease, but also fatigue occurs
untimely. Obvious for the fragility being
coursed by stress crack. Rustiness can also
decrease the elasticity for wire rope. At
present, the quantitative evaluation for wire
rope rustiness lacks the effective means. Here,
we are on the basis of the basic principle for
the wire rope magnetic testing, put forward
adopting. Equivalent rusting concept to achieve
rustiness quantitative evaluation. By the
Equivalent Rusting Concept we mean proceeding
from the wire rope intensity, analyze the
different rustiness degrees have influence upon
the wire rope intensity. To combine the magnetic
testing result and give out a quantitative
target, ascertain the application state for the
wire rope. Make a analysis in the concrete,
inspect out the pitting etc local flaw of wire
rope with leakage magnetic field testing method.
Taking their signal intensity and feature are
compare with the broken wire signal, ascertain
the wire rope concern between the pitting degree
and broken wire number.
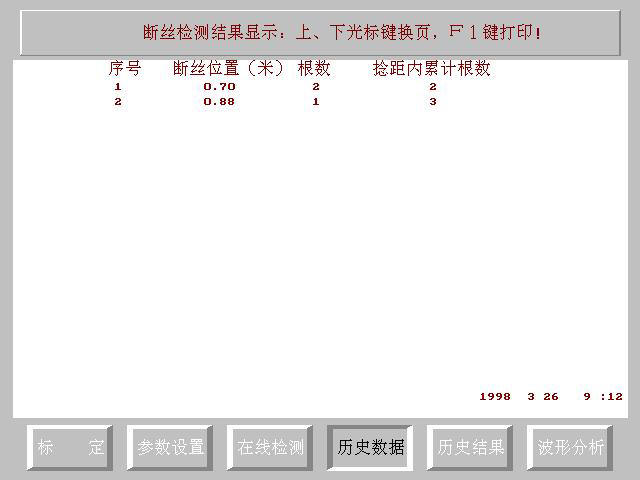 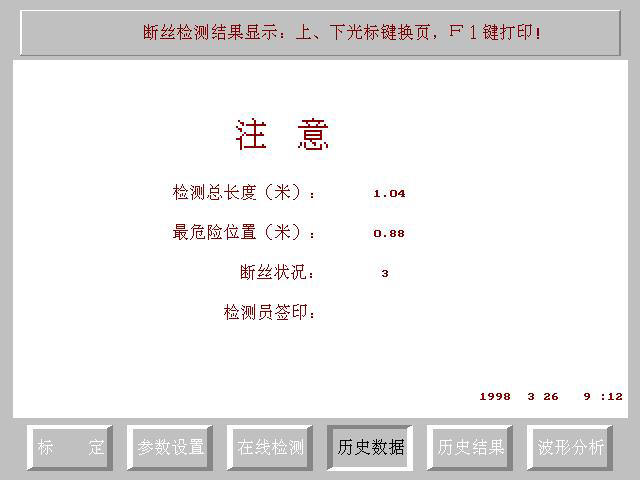
Adopt
magnetic bridge circuit principle inspect out
the corrosion etc, large areas flaw for the wire
rope, ascertain after the rustiness, the
efficacious metallic cross-sectional areas to
combine the intensity theory and give out the
practice load bearing cross-sectional areas.
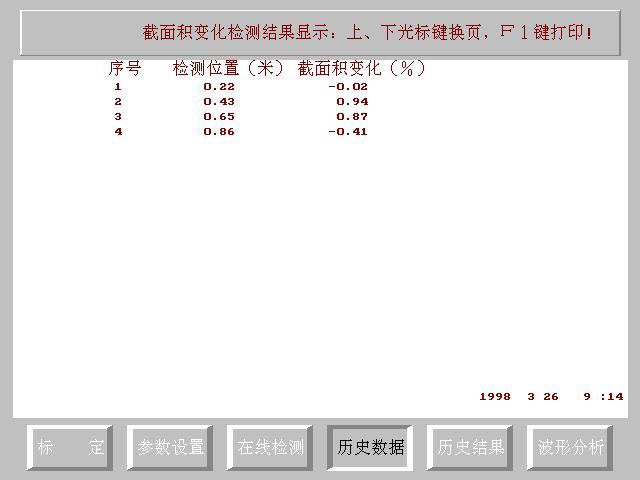 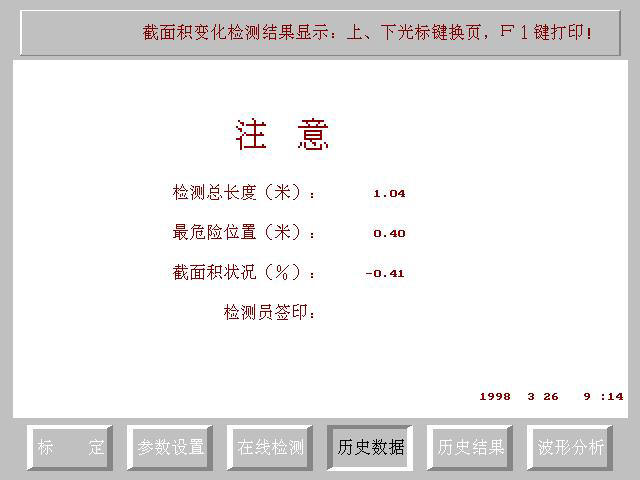 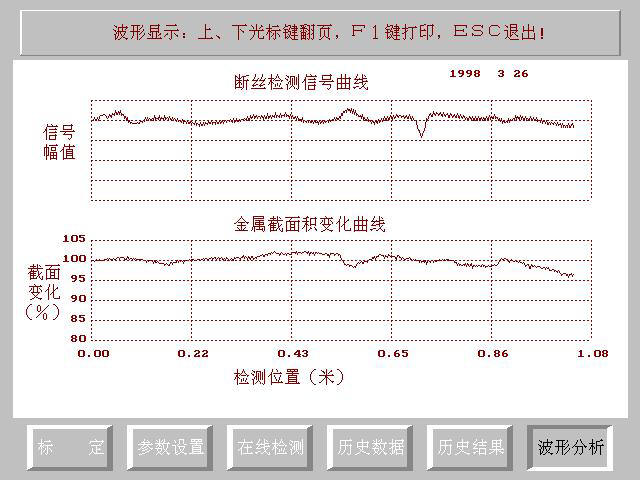
(4)
The evaluation of testing results for wire rope
state
The
aim of wire rope testing is that not only
obtains the geometric parameter of overall
accuracy, but also provides the requisite
parameter of wire rope intensity, lifetime
evaluation, proceeding to provide the basis for
practical wire rope change. There fore, it is
necessary/reasonable that the testing result
would enable to be connected with the requisite
parameter for the wire rope evaluation. At
present, evaluating wire rope state start with
wire rope intensity respect in general. However,
the difference of accepting force and scrap
condition for wire rope are very great for the
geometric shape complexity and the application
condition change of the wire rope, thus, the
evaluation of the wire rope intensity lack the
parameter with instrument testing. The internal
and external department concerned evaluates the
wire rope major basis with wire rope testing
result basically. And then combine with damaged
experimental result of the wire rope. Here, we
ascertain the wire rope state with the practical
metallic loss as the major target. Here, by
practical metallic loss is meant the loss of
wire rope metallic function including the flaw
of broken wire, abrasion, rustiness, fatigue
etc. This loss is corresponding with the certain
testing signal of the wire rope.
①
Evaluation basis of non-destructive testing for
wire ropes
It is
known to all that the important feature for wire
rope cant be disrupted suddenly. Because of the
complexity for wire rope structure, it bears the
combining action such as stretching, bending,
squeezing, torsion, etc. in the course of
manufacture. There fore, the wire rope bears
force state very complex. Every piece of wire
rope is composed with some dozen of wires. It is
a statically indeterminate system many scholars
desire to solve the each wire internal force
with high order partial differential equation,
precede to evaluate the operation life for wire
rope. But, it is very different to use in
concrete practice. They have many influence upon
the operation life factor for wire rope such as
stress (wire rope stress), in proportion as the
diameter between wheel and wire structural form
and material quality for the wire rope, twining
technique, lubricating condition, environment
temperature, glide wheel material quality, rope
score shape of glide wheel. Etc. It is difficult
for many factor to calculator the operation life
with a formulation accurately. There fore, every
country is grounded on experiments and
industrial application experience to ensure
selecting wire rope with enough statically
intensity. This brings about many problems for
the application safety of the wire ropes. There
fore, the experimental research results for wire
rope testing (destructive or non-destructive
testing) pay an important part in the design,
manufacture, application and maintenance.
1)
Failure model for wire rope
The
main destructive reason for wire ropes is divide
into three kinds of corrosion, abrasion and
fatigue. Because of the three factors common
action result, the wire rope failure is none
other than broken wire, broken strand and
diameter shrink. Lead to decrease the intensity
of the wire rope. At last reach the ultimate
tensile strength and then destruction. In
general speaking, after hanging a new wire rope.
Soon, the structure of the wire rope becomes
inseparable. The loads distribute even in the
wire rope. At same time, counteract the internal
stress between supporting force of wire ropes
each other, increase the number of disruptive
wire at the some time. As a result, increase the
breaking pulling force, and then, the intensity
of the breaking pulling force becomes low
gradually. To the certain extent that the wire
rope disrupt suddenly. According to analysis as
mentioned before, combine with the practical
application
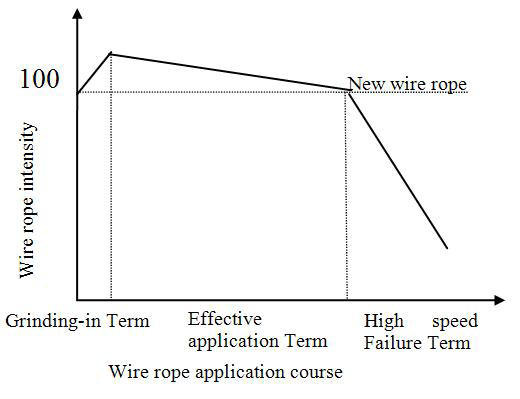 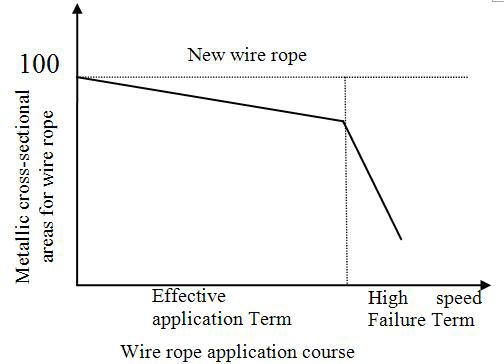
State, adopt as shown in Fig. 2-19 model as the
failure model for wire rope application.
2)
The intensity analysis for wire rope
During the practical application course for wire
rope, the research analysis of wire rope failure
concerned express: with the increment of
application time for stretching resistance
strength of wire rope, produce the stretching
resistance strength for wire rope decrease for
the wire rope selection type consider the
influence of the endurance
Bending strength and impact resistance load
strength in the course of wire rope destruction.
There fore, during the course of application, by
the wire rope intensity mean the whole breaking
pulley force for wire ropes. According to the
intensity standard for the wire rope, the whole
breaking pulling force for wire ropes Sb
(Breaking Strength) are:
Sb=KSa (2-6)
Where, Sa (Aggregate Strength) is the
whole wire aggregate breaking force in the wire
ropes, K is the coefficient for wire ropes, the
quantity (large or small) of value K come
under the influence of the wire rope structure,
lubricating condition and the influence of
stress state in the wire rope.
The
contact stress between wires in the wire rope
can analyses on the basis of hertz (HZ)
formula. Before the wire rope without bearing
load, the contact relationship is shown in Fig.
2-20 (a). their contact area is zero. After
pressure action, the contact position produce
deformation as shown in Fig. 2-20 (b)
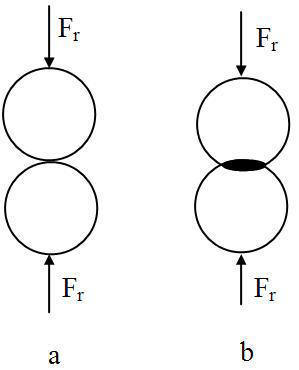
Fig. 2-20 The analysis schematic Diagram for
wire stress
The
contact line becomes the contact surface of
rectangle, and the contact point becomes a
ellipse (or circular) contact surface. Every
point on the contact surface produce the contact
stress according to certain regular distribution
is relevant with deformation quantity. According
to the research for elasticity mechanics, can
know that the abrasion of wire rope don’t occur
at that time, the contact stress increase
between the wires. The axial component force of
this stress. Counteract on the axial pulling
force of wire rope. The result is that the whole
rope breaking pulling force of wire rope is
fewer than all wire aggregate breaking puling
force in wire rope. When wire rope increment
between the wires. The contact stress increase.
It expresses the value K increment. These
decreasing contact stress remedy the intensity
for wire rope abrasion decrement. (Sw
decrement). According to (2-6) equation, we
know. The result is that the whole rope breaking
pulling force of wire rope change isn’t great
during the whole wire rope efficacious
application term. But at the later period of
application, because of Hertz (Hz) stress
increment to about zero. At that time, value
K is definite value. While Sa
increase continuously, decreasing contact stress
can’t neutralize the wire rope intensity loss of
continuous increment. This causes the sudden
failure of wire rope. Because of the complexity
of pulling stress, bend stress, etc in the wire
rope, it isn’t impossible that estimate or
decide the contact stress for wire rope
intensity influence. There fore, the
non-destructive testing method can’t determine
the breaking intensity for the whole rope of the
wire rope. And as analysis before, we know that,
the breaking intensity for the whole rope of the
wire rope can’t explain the wire rope safety.
So, must seek the parameter that can inspect and
explaining wire rope safety.
3)
The assessment target for the wire rope
intensity loss
Let
wire rope bearing load, is P, P
can change under Pmax context. Let Sb
is the breaking pulling force for the whole rope
of the wire rope, Sb can change above
Sbmin context. When the following equation
is tenable, the wire rope can use safely.
Pmax < Sbmin (2-7)
As
analysis before, we know, when the wire rope is
a new one, because of the lubricating state and
other state min the wire rope without damage, so
that value K is the smallest Namely Kmin
= Knew
It
follows from (2-6), we know that the loss of
breaking strength for whole wire rope (LBS)
is:
LBS
= Sbnew
(1-Sb/Sbnew)
its
percentage of the relative loss strength is:
LBS%
= LBS/Sbnew×100= (1-Sb/Sbnew)×100
The
loss of aggregate strength (LAS) is:
LAS = Sanew
(1-Sa/Sanew)
its
percentage of the relative loss strength is
LAS%
= LAS/Sanew×100
=
(1-Sa/Sanew)×100
The
action of scrap criterion for wire rope is that
guarantee from sudden breaking before next
testing. Suppose wire rope proceed with testing.
According to equation (2-7), we obtain Pmax <
Sbmin (i) = KminSa(i) = KnewSa(i)
LBS(i)%=[1-Sb(i)/Sbnew; So
that
LBSmax(i)%=[1-Sbmin(i)/Sbnew ]*100=
[1-KminSa(i)/KnewSanew]*100=[1-Sa(i)/Sanew]*100=LAS%
Therefore, the greatest breaking pulling force
loss or aggregate breaking pulling force loss
for wire ropes can be used as the scrap standard
for wire rope. This makes a great difference
from the breaking pulling force in general
significance. During the application of the wire
rope, cuttiga section of wire rope makes an
experiment on damage. Because of the possibility
and conventionality of operation, cutting the
section of wire rope can’t ensure on the
location of the weakest part. It is very
dangerous to judge the whole wire rope strength
with this data. The above equation is on the
basis of equation (2-7). Only when calculate the
greatest magnitude of wire rope strength loss,
can you evaluate the wire rope state. We know
from equation (2-8) the greatest strength loss
for the wire rope is, in the final analysis,
loss for aggregate strength. The equation
eliminate magnitude wire rope coefficient K. if
made certain of breaking strength in every piece
of wire, we should acquire the wire rope state.
According to this target, if adopt the suitable
testing instrument, should understand the damage
state of wire rope in the cross-sectional area
in detail and the location and number of damage
distribute state in the whole wire rope testing.
According to its concentrative degree, judge the
efficacious cross-sectional area size at the
weakest location in the whole length and reduce
quantity on the location of wire rope.
②
Evaluation of broken wire testing for wire ropes
1)
The cause of broken wire produce
During the application for long time, the wire
rope metallic fatigue is caused by the wire
beardy again and again, extruding under the
power pulling force. When the bending and
extruding reach certain times, in addition
abrasion, the wires would break when the number
of breaking broken wire reach certain number,
the wire rope scrap, would change a new rope.
Broken wire occurs to the middle and later
period for wire rope application.
The
wire ropes for broken wire scrap possess the
following feature:
(a)
The operation life is shorter
(b)
Under the general condition, the abrasion and
rustiness are lighter.
(c)
The wire rope scope of application is that
position that by pass pulley or spool is acted
by stretching load with broken wire as scrap
standard wire rope mainly.
2)
The influence of the broken wire for wire rope
strength
After
the wire rope occur to broken wire, would the
cross-sectional area for wire rope decreasing.
Make its pulling force reducing. The reducing
number and broken wire amount are related to
distribution. Experimental evidence: The
reducing of breaking pulling force for wire rope
is certain proportional to the broken wire rate
within 30% broken wire rate. If the broken wires
distribute the whole length, don’t concentrate
within a length of lay, the influence is very
small for whole rope breaking pulling force.
There are great difference between dispersing
every strands and concentrating a strand within
a length of lay. Make out from table (2-4)
(variety of experimental wire rope is 6×24.
The broken wire method is artificial cutting on
the new wire rope). If the broken wires
concentrate in a strand, the pulling force
reduction is more doubled and redoubled change
than dispersing in every strand. The
stipulations in every regulation allowable
broken wire number refer to distribute within
every strand of a length of lay. If the broken
wires concentrate on a surface of a strand,
broken wire allowable number would decrease
about one half.
Table 2-4 The broken wire and location for
influence of breaking pulling force
Broken wire
number |
Broken wire location |
Pulling force %
Reducing Rate |
14(about 14%) |
Concentrate in a
strand, on a surface |
26.6 |
Disperse within three
length of lay |
2.3 |
Disperse on the same
cross-section of wire rope in every
stand |
9.6 |
Disperse within three
length of lay |
3.6 |
30(about 20%) |
Concentrate in two
strand, on a surface |
42.2 |
Disperse within three
length of lay |
5.0 |
Disperse on the same
cross-section of wire rope in every
stand |
21.6 |
Disperse within three
length of lay |
3.7 |
42(about 30%) |
Concentrate in two
strand, on a surface |
43.1 |
Disperse within three
length of lay |
6.2 |
Disperse on the same
cross-section of wire rope in every
stand
disperse within three
length of lay |
27.5 |
Above-mentioned experiments are proceeding in
the laboratory. Worksite practice proves that:
During the operating of the wire rope. Not only
occur to external broken wire but also does the
internal broken wire. The distributing condition
is different form the internal and external
broken wire for the wire rope.
There
is great difference between the two for the wire
rope structure and operating condition are
different. The whole rope abruption and
dynamic-load impact experiment express that
proceed the worksite scrap wire rope:
The
scraping part in scraped wire rope such as
abrasion and rustiness are lighter. The
reduction of whole rope breaking pulling force
is caused by the broken wire section decrement
mainly. There fore, the percent broken wire
section area plus within a length of ply of wire
rope with its total section area proportion
namely can look upon the percentage of strength
decrement. This also proves evaluation formula
correctness above-mentioned relative wire rope
strength. The correct implication for the broken
wire quantitative testing of the wire ropes
would be that. Broken wire quantity isn’t broken
wire number. The broken wire quantity is none
other than the percent of the sum total for the
different wire diameter broken wire sectional
area within a length of lay. This implication is
embodied in Hoisting machinery safety regulation
(State Standard GB6067-85) clearly. This norm
stipulat. When safe coefficient is fewer than
six, the scrap broken wire number of wire rope
is 10% of the sum of total. When safe
coefficient is between six and seven, the scrap
broken wire number is 12%. When safe coefficient
is more than seven, the scrap broken wire number
is 14%. In addition, the scrap broken wire
calculate with thin wire entirely. A piece if
thick wire in the wire rope is corresponding to
1.7 piece of thin wire. For example, 6×Fi(29)filled-system
wire rope, when safe coefficient is more than 6,
the scrap broken wire number of wire rope
calculate according to the following method: 6
strand
×
(22 pieces of thick wires
×
1.7+7 pieces of thin wire)
×
12%
÷
1.7 = 18 pieces of the wires .
All
these require us that must be considered with
designing the sensor for broken wire testing for
wire ropes and distinguishing the broken wire at
that time.
3)
The
evaluation of the broken wire testing result
The
aim of non-destructive testing for wire rope
isn’t only acquiring the result of broken wire
testing. It is very important for testing result
to evaluate wire rope state. In order-to provide
scientific basis for the maintenance and
reasonable change of wire rope. As analyzed
before, we know that the percent of broken wire
within unit length (refer to a length of lay in
common) will influence the strength and
operation life for the wire rope seriously. The
less broken wire concentrating area the more
strength influences degree. But make out from
the practical condition, unbroken wire make
broken wire under stress state for their
occurring coulomb frictional force between each
wires in the wire ropes.
The
broken wire stress is on the basis of the
certain regular distribution, in a section of
area, reach normal value gradually. What is
called broken wire efficacious length is the
stress reaching normal value? Over efficacious
length is considered that the stress value of
wire rope is all the same to normal condition.
The research for the broken wire efficacious
length express, when lifting wire rope testing,
we have a disregard for the load capacity of
broken wire generally. In this way, don’t
consider that the broken wire efficacious length
to make the testing result towards safe.
The
research express that, the prominent feature of
un corroded and un abrasion wire rope is almost
tensile strength without reduce. There is little
difference between new and old wire rope
breaking force, in many experimental result.
Only when the individual sample fold wire rope
is with other factor little influence, or
individual wire exist as fatigue flaw can it
make the breaking tore decrement. The breaking
force for wire rope (or tensile strength)
reducing value is also within 5%. There fore
concentration breaking force the broken wire
decreasing efficacious metallic cross-sectional
areas mainly for the tensile strength reducing
very little causes reducing. As a result, with
the decrement of the efficacious metallic
cross-sectional number, is corresponding with
the concentration breaking torle-decreasing
umber. However, the broken wire can’t produce in
the same cross-sectional entirely. There fore,
the sum of broken wire cross-sectional areas
within a length of lay for wire ropes can
consider the decrement value of wire rope
efficacious cross-sectional areas. In this way,
we can calculate wire rope strength loss on the
basis of broken wire condition within the length
of lay. If ignore tensile strength change of
wire rope, the new wire rope is related to
broken wire strength loss of wire rope by the
following:
LAS%=F% (2-9)
Where
f% is loss coefficient of metallic
cross-sectional areas, within length of lay.
Namely, there occur percent of the whole wire
rope cross-sectional areas within broken wire
areas for length of lay. The wire rope made by
twisting equal diameter wire, it is equal to the
percent of length of lay broken wire.
Here,
we consider that the broken wire state has
influence on wire rope state within a length of
lay mainly. After adopting non-destructive
testing technique acquire the broken wire state
on the every location of wire rope, combine with
the length of wire rope diameter, length of lay,
the diameter of wire and type etc, the structure
feature and the historical condition of the wire
rope, the experience of users. It is not
difficult for us to give out the wire rope
state, suitable main tenure method, next testing
time and correct scraping time etc.
③Evaluation
of abrasion for wire ropes
1/
The cause of abrasion production
When
wire rope abrades in the operation, it get into
touch with other object and relative motion to
produce frictional force. Under the action of
physics and chemistry., abrade the surface of
the wire rope continuously. The abrasion is
commonly recognized damage form for wire rope.
Take petroleum industry for example, and
according to investigation, it is abrasion that
the oil use failure form mainly for wire rope.
But up to now have had not a calculating method
enabling to ascertain the abrasion degree for
wire rope. At abroad, adopt the evaluation
method for wire rope abrasion commonly: one is
on the basis of testing the surface of the wire
rope, the other is on the basis of the
application namely, the product of bearing load
for wire rope and operation stroke. The former
carries with the artificial factor and evaluates
the internal abrasion without method.
The
latter is applied to small changes of wire rope
load, but it is very difficult in fact.
2)
The classification for wire rope abrasion
The
abrasion of wire rope is divided into the outer
abrasion and the internal abrasion and deformed
abrasion. There are two kind of monocyclic
abrasion and whole cyclic abrasion in typical
outer abrasion. As shown in 2-21. this kind of
abrasion produce the efficacious metallic
cross-sectional areas decrement and is related
to outer contact condition mainly. However, the
effect of the deformation and internal abrasion
on the metallic cross-sectional areas for wire
rope isn’t great.
The
deformed abrasion is cause by the vibration and
collision. There other object, the hoist lifting
wire rope, hits produce the surface abrasion of
wire rope such as wire rope of roller surface.
After deformation and abrasion, the extents of
wire become wide. The wire rope is easy to
break, even if the cross-sectional areas of wire
rope decrease smaller because of the hardened
surface on the wire rope. During the course of
wire rope application, the curvature radius of
each wire can’t be all the same. There fore,
each wire in the wire rope can produce action
force each other and occur to slide, forming
internal abrasion. The condition takes place in
the wire rope of multistory structure. Because
of the producing and development of the internal
abrasion, deformation abrasion and rustiness at
the same time, and the effect on the metallic
cross-sectional areas for wire rope change isn’t
great. It reflect feature in magnetic testing
signal that isn’t obvious. There fore, it is
more difficult for internal abrasion and
deformation a bras into. Detect and evaluate,
must combine with influeme of other factor. We
will illustrate in the rustiness parts in
detail. In the falling, first of all
Discuss outer abrasion state evaluation.
Monocyclic abrasion whole cyclic abrasion
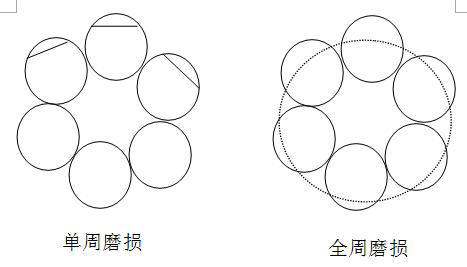
Fig.
2-21 outer abrasion for wire rope
3)
The effect of wire rope abrasion on strength
According to abrasion experimental result of
wire rope, we know, as shown in Fig 2-22 under
the condition of the wire rope along
circumferential abrasion, before the wire rope
break, many abraded wire ropes have broken, when
abrasion strength decrease, the decrement rate
of cross-sectional areas are near the strength
reducing rate. But after the abrasion increase
the strength reducing seems to rise. Under the
local abrasion condition, after wire rope break,
the decrement rate and strength-reducing rate
are almost the same.
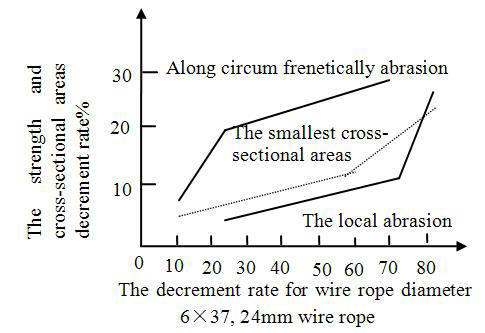
4)
The evaluation of abrasion state for wire rope
according to the effect of wire rope abrasion on
strength, combine with equation (2-6). The
evaluation of wire rope diameter, if the wire
rope diameter changes make not much difference
in every direction, can consider that is caused
by the abrasion circumferential abrasion, if the
wire rope diameter change value makes much
difference in two-curtain direction. Can
consider that monocyclic abrasion, according to
above sectional analysis, we obtain.
LBS%max=LAS%=LMA%
(2-10)
Namely, the decrement quantity of wire rope
cross-sectional areas is equal to the greatest
loss for wire rope strength. The circumstance is
more complex for the circum frenetically
abrasion as show in Fig. 2-23. Take 6×7Fc
structure wire rope of Cross-sectional areas
loss3% for outer layer wire for example, in
order to determine all wires concentrating
breaking force in the wire rope, must consider
that each strand superficial lager wire in the
wire rope all show up the helix structure. Every
superficial lager wire will all appear as shown
in Fig. Location along wire rope axial length
direction. To consider a range with a far fewer
resemble length, all 36 pieces of superficial
layer wires will have an effect on wire rope
concentrating breaking force, but it is not the
only one that is shown in Fig. Six pieces of
wires.
This
means that this kind of structure wire rope. At
that time, the percent of wire rope
concentrating breaking fore was none other than
LAS%= 6×6×30%/6×7
=25.7% but, it was not LAS%= 6×30%/6×7
=4.3%
There
fore, we introduce the concept of reservation
strength (Sr)
The
definition of reservation strength is the sum of
all wire breaking force besides the superficial
layer in every strand. According to this
definition, for 6×7
FC structure, we have; Sr%=1/7=14% to wire rope
strength state of circum frenetically abrasion
we have a calculating formula in the following.
(LBS%max) y2, (LAS%)y2, (LMA%)y2 refer to wire
rope the greatest breaking force loss is caused
by circumferential abrasion, wire rope
concentrating breaking loss and metallic
cross-sectional areas loss individually.
④Evaluation of rustiness for wire ropes
1/
The cause of rustiness production
The
wire ropes use in the open air commonly. The
sun-scorched and rain-drenched can corrode the
wire rope. The corrosion makes the damage to
wire ropes very seriously especially under the
odious circumstance of the harmful gas,
seawater. The abraded surface of wire rope
exists as difference of oxygen nelerocyclics. It
makes the certain local metal on the surface of
wire rope into positive pole, the other near
local metal into negative pole. In this way,
form mass mini type battery. Under the action of
the mini type battery, the surface of wire
becomes many circular corrodible pits and
deepens gradually. These pits become the
concentrating points of the stress, the source
of the fatigue flaw. At the same time, the
corrosion decreases the cross-sectional areas of
wire rope and reduces the elasticity and
capacity of bearing impact load. Lead to wire
rope scrap at last. According to the
introduction of material concerned, 70~80% scrap
wire rope is caused by corrosion, as for the
fatigue breaking of deserving move attention is
only 10~15%, under the common condition, the
operating life difference between the fat
liquoring and without fat liquoring is one
times. At present, the wire ropes operating life
in the hoister is form 2 to 3 years in our
country. The wire rope operating life in
water-drenched serious mine reduce three months.
Not only waste materials and staffs, increasing
production lost. But also influence production,
producing accident for the wire ropes change
frequently.
The
rustiness of wire rope is divided into the outer
rustiness and the internal rustiness. At
present, testing rustiness can only adopt the
methods of visualization and percussion. The
internal rustiness testing is more difficult
than external rustiness testing commonly adopts
the following methods: A. Try to twist off
between the strands of wire rope B. whether the
diameter of wire rope is uniform or not. For
example, if apiece of wire rope is internal
rustiness, the diameter of passing through the
wheel parts is reducing, but not to passing
parts become thick. C. Konck at the wire rope
hearing testing with little hammer knocking. If
hear the “click” sound, this means internal
rustiness in the wire rope. D. Internal decrease
between outer layer strands, happen to broken
wire in concave location of wire rope strand, at
the same time.
2/
The effect of rustiness on application function
of wire ropes wire rope strength. It is far more
than broken wire and abrasion. For example, mine
owner shaft of Sanjialin, Zaozhuang County, in
Shandong Province, it is neither broken wire nor
wire rope diameter decrement. The wire rope
strength reduces 22-27 percent. At present and
later, when many mine change wire rope, both
length of lay and whole rope broken wire aren’t
more, at present, not to find suitable method to
measure the rustiness degree with quantitative
concept for the effect degree of rustiness on
wire rope strength is far more complex and
serious than broken wire and abrasion. In order
to analyses convenience. The rustiness degree of
wire ropes in table 2-5 is divided into four
grades and briefly evaluates the effect on
mechanical function.
Table
2-5 Grade of Rustiness
Rank |
Surface Rustiness Degree for Wire Rope |
Loss of Mechanical Function |
Mila (I) |
Wires change the oolour, lose sheen,
exist at scale or rusty spot (appear to
minikin black point on the surface of
the wire rope) |
Abort 10% |
More serious (II) |
There are scales or pits on the surface
of wire ropes, but isn’t connected yet. |
10~25% |
Serious (III) |
Existing rustiness flaw, the rusty spot
become pits are connected and form rusty
minikin ditch. Outer layer wire
tottering. |
25~40% |
Dangerous (IV) |
The rustiness areas are larger, the wire
lose circle, the iron mold gnaw into
1/3~1/2 depth between strand wire
|
Over 40% |
|
Fig 2-23 6×7FC
circumferential abrasion schematic
Diagram for wire rope |
|
We
can make from above table, the Rank (I) belongs
to the Mile Rustiness. The rustiness effect
isn’t great, can scrap on the basis of other
stipulation. The Rank (II) rustiness would be
considered the effect of the rustiness. The Rank
(III) rustiness is serious rustiness. When reach
Rank (III), the application isn’t safe. While
the Rank (IV) has been in the dangerous state.
3/
Evaluation of Rustiness
Take
one thing with another, such as discovering
rusty spot with LF, discovering the mild
rustiness in advance, providing suitable
protective method. The key is the quantity
quantization of LF signal and LMA signal with
LMA testing serious rustiness to prevent the
accident happenstance.
The
rusty damage isn’t also independent existence in
productive practice. It is always related to the
equipment condition of application department,
natural circumstance, maintenance, and
management. It produces with fatigue and
abrasion at the same time. There fore, it bring
very difficult to evaluate the rustiness. Here,
we put forward a comprehensive LF, LMA signal
feature, proceeding to evaluating method, for a
wire rope state. First select a section on the
wire rope on testing, proceed to calibrate the
signal in the section of wire rope. Ascertain
the base line of LF signal and LMA signal
individually.
When
there occur rustiness flaw in the wire rope,
on the one hand, the magnetic function in
every parts of the wire rope have taken place
changes for rustiness degree isn’t uniform. This
reflecting in LF signal is the increment of
sudden changes. Back ground noise frequency with
overlying signal increase. At that time,
according to LF signal, distinguish broken wire
decrement. But practical state that produce
broken wire signal isn’t broken wire. There
fore, we call it is equivalent broken wire fd.
Distinguish software and equivalent broken wire
number with broken wire quantity according to
the broken wire evaluation formula. We have:
(LAS%)d=(f%)d
(2-12)
Where
(LAS%)d refers to the concentrating strength
loss for wire rope is caused by the equivalent
broken wire.
(f%)d
is the equivalent broken wire number for wire
rope According to above-mentioned formula we can
calculate the wire rope strength state with LF
signal ascertainment.
On
the other hand,
production of rustiness makes the metallic
cross-sectional areas for wire rope relative
increment. The oxidation and vulcanization etc
for wire rope make the overall magnetic
inductivity decrement of LMA measured value. If
we consider the complicacy of rustiness existing
condition and abrasion, we adopt the evaluation
formula of circumferential abrasion strength
calculating strength loss is caused by the
rustiness. Namely,
(LBS%max)dy=(LAS%)dy= (LMA%)dy/Sdr% ×100
(2-13)
Where, (LBS%max)dy,(LAS%)dy,(LMA%)dy, refer to
wire rope the greatest strength loss is caused
by rustiness, wire rope concentrating strength
loss and equivalent cross-sectional areas loss.
After two aspects consider comprehensively, we
obtain the wire rope strength loss is caused by
the rustiness:
(LBS%max)x = (LBS%max)d + (LBS%max)dy (2-14)
According to this formula, after acquiring the
signal LF and LMA, pass through the evaluation.
We can know that the wire rope strength loss by
rustiness produces.
The
main technical parameter
The
diameter is tested:
φ1.5~200mm
The
relative speed of the sensor between the wire
ropes 0.0~6.0m/s
Optimum speed: 0.3~1.5m/s
The
interstices of the guide bush in the sensor
between the wire ropes: optimum distance: 2~6
The
detected capability broken wire flaw (LF):
Qualitative: The accurate rate of on the point
of concentrated broken wire qualitative test:
99.99%
Quantitative: There is a permissible error of a
piece of wire or a equivalence on the point of
Concentrated broken wire number.
There
are no errors the quantitative testing more than
100 times on the point of Concentrated broken
wire number.
The
accurate rate≥92%
The
detected capability of the quantitative change
rate of the metallic cross-sectional areas
(LMA):
The
repeatability allowable error of the testing
sensitivity:
±0.055%
The
allowable error of the testing accuracy rate
indicated value:
±0.2%
The
detected capability of the location (L):
The
indicated value percent error of the testing
length:
±0.3%
The
electrical supply:
The
supply electrical power for the computer batter
5V
The
specifications in common use <10Kg
4.
The Results of Laboratory
(1)
The
Explanatory Notes of Technical Terms
The
accurate judge rate for wire ropes refer to the
quantitative testing instrument for wire rope
inspect the accuracy for the broken wire number
within its qualitative distinguishing scopes.
That
is to say that the quantitative testing
instrument distinguish the broken wire number to
conform to practical broken wire number for wire
rope degree.
The
change testing accuracy for cross-sectional
areas refer to the change quantity of testing
signal for the wire rope is caused by the change
of wire rope per unit areas.
(2)
The
experimental results of broken wire and abrasion
for wire rope
①
Testing Method
Our
designing sensors possess the function of
integration with broken wire testing and
cross-sectional areas testing. There fore, the
broken wire experience and cross-sectional areas
experience are synchronization. Whether or not
it exist as broken wire with being tested wire
rope magnetization, sensitive element testing
leakage magnetic field in broken wire location
of wire rope. Analyze the leakage magnetic field
waves with computer and relative software. Go
further and judge the broken wire number with
photoelectric encoder ascertain relative the
location of broken wire. Inspect the
cross-sectional areas change for wire rope with
magnetic flux change testing in wire rope. After
calibration of wire rope cross-sectional areas,
achieve cross-sectional areas for wire rope
quantitative testing. At the some time, testing
signal input computer analysis. After computer
analyze, print the result (including the
location of wire rope, broken wire number)
checking with practical condition. According to
above-mentioned condition, calculate broken wire
quantitative accurate rate, differentiate error
of broken wire location. According to after
calibration sensor proceed to experience
ascertain the abrasion quantity testing error
range of cross-sectional areas for the wire
rope.
②
Testing Condition
First
of all, is analogue of wire rope flaw state?
Because of condition limit, we have only a piece
of
φ24(6×7)wire
rope, sampling rope. Broken wire analogous state
is shown in Fig. 4-1. Broken wire fracture
interval of A and B place is 2mm. Broken wire
state of location C is internal broken wire in
Figure.1
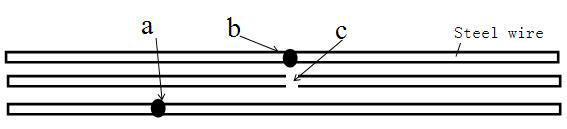
Fig. 4-1 Analog broken
wire schematic Diagram for Wire Rope
Because of the magnetic testing principle,
cross-sectional areas change testing experience
proceed in twice: Fix sensor in certain part of
the wire rope, then increase the cross-sectional
areas change of wire analogue wire rope between
this part of strands for wire rope. According
these experimental results, ascertain the
testing sensitivity of the cross-sectional areas
change. Increase the typical signal output
waveforms of cross-sectional areas for wire
analogue is shown in Fig. 4-2,
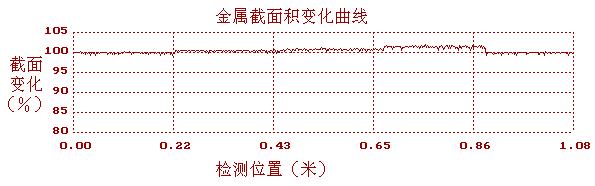
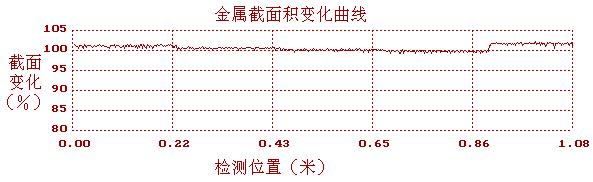
Fig
4-2 The signal output waves of cross-sectional
areas change for wire rope
At
first, there isn’t any wire in the wire rope in
the course of experience for Figure (a), and
then increase from 1.2. until 3 pieces of the
wire rope. Finally, take any all 3 pieces of the
wire ropes, the diameter of application wire
rope is 4mm. In the course of Experience Figure
(b) is at issue with Figure (a). The curve in
the Figure according to the principle of the
parts of second introduction, proceeding to
calibration. Achieve the quantization.
2/
Take a certain length on the wire rope
proceeding repeatability experience, to
ascertain the error range of instrument.
④
Testing Results
1/
Testing results of broken wire for wire rope
vide Table 4-1
2/
Handling results of data statistics for broken
wire vide Table 4-2
3/
Handling results of data statistics for abrasion
quality testing of cross-sectional areas vide
Table 4-3
Table
4-1 Testing results of broken wire for wire rope
Order number
|
Situated L1 |
Situated L2 |
Order number |
Situated L1 |
Situated L2 |
Location
(Meter) |
Broken wire number
(sticks of) |
Location
(Meter) |
Broken wire number
(sticks of ) |
Location
(Meter) |
Broken wire number
(sticks of) |
Location
(Meter) |
Broken wire number
(sticks of) |
Table 4-2 The statistics analysis results of the
accurate judge rate for wire rope broken wire
Misjudge umber
Practical number |
-2 |
-1 |
0 |
1 |
2 |
Total |
1 |
|
2 |
48 |
|
|
50 |
2 |
|
2 |
47 |
1 |
|
50 |
Total |
|
4 |
95 |
1 |
|
100 |
Average(%) |
|
4 |
95 |
1 |
|
100 |
Analyze calculating
result expression: Occurring no
misjudgment, broken wire quantitative
accurate judgment rate is 95%. Occurring
for allowable misjndgenent of a stick of
wire rope, broken wire quantitative
accurate judgment rate is 100% |
Table 4-3 The testing results of cross-sectional
areas change for wire rope
Order number |
Segment L1 cross-sectional areas change
(mm2) |
L2
(mm2) |
L3
(mm2) |
L4
(mm2) |
Order number |
Segment L1 cross-sectional areas change
(mm2) |
L2
(mm2) |
L3
(mm2) |
L4
(mm2) |
Analyze calculating result expression:
Adopting this principle can achieve the
testing error <±0.05% |
5. Reference Literature:
(4) Yang Shuzi, Kang Yihua “Quantitative
inspection for broken wires of wire ropes
principle technique” Peking, National defense
industrial publishing house.
(6) Chu JianXin. GuWei “The fluxgate testing
method of leakage magnetic field for wire rope
flaw”《instrument
and apparatus Journal》
P437~P440, 18(4), 1997.
(7) GuWei, ChuJianXin “Testing sensor for a type
of the fluxgate wire rope flaw” P226~234, 19(8),
1997
|